What Size Tank for Beer Fermentation?
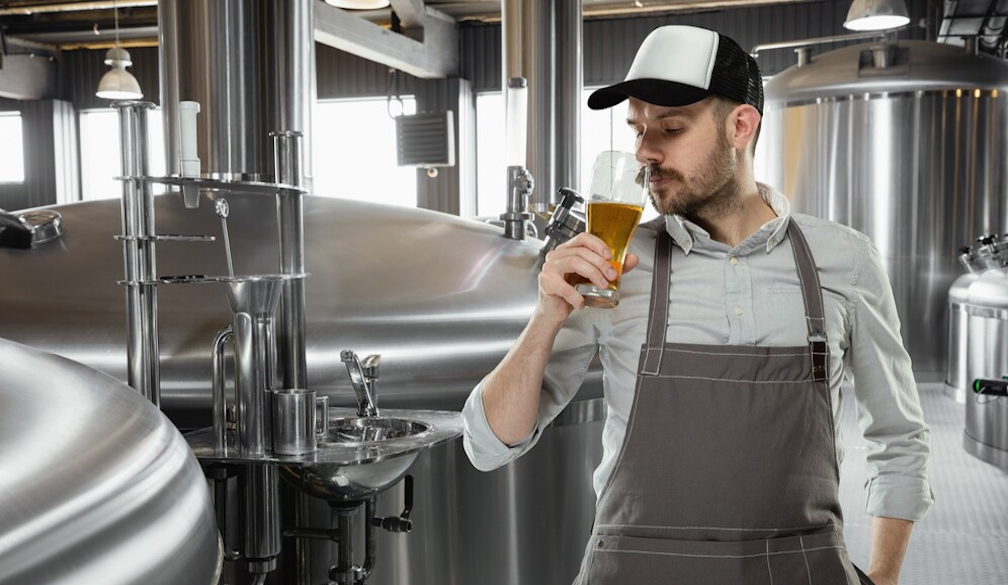
Choosing the right size tank for beer fermentation is a crucial decision that can significantly impact the brewing process and the quality of the final product. Whether you're a home brewer or running a commercial brewery, understanding the factors that determine the appropriate tank size is essential. This article will explore the most relevant questions related to selecting the right fermentation tank size, providing insights into how to make the best decision for your brewing needs.
Get a turnkey solution for brewery equipment
If you plan to open or expand the brewery, you can contact Micet Craft directly. Our engineers will design and manufacture brewery equipment according to your brewing process. Of course, we will also provide you with a complete turnkey solution. Also, if you have any questions related to beer equipment, you can visit Micet Group to seek solutions.
Visit Micet Group official website: https://www.micetgroup.com/
How Does Batch Size Influence the Choice of Fermentation Tank Size?
The size of your brewing batch is one of the primary factors in determining the appropriate size for your fermentation tank. Different batch sizes require different tank capacities to ensure optimal fermentation conditions.
Home Brewing vs. Commercial Brewing:
For home brewing, batch sizes typically range from 5 gallons to 20 gallons. A 7-gallon to 15-gallon fermenter is usually sufficient for these batches, allowing for adequate headspace for fermentation activity. Commercial breweries, on the other hand, deal with much larger batches, often ranging from several barrels to hundreds of barrels. In this case, fermentation tanks can range from 3-barrel (93 gallons) tanks for small brewpubs to 100-barrel (3,100 gallons) tanks for large-scale breweries.
Headspace Considerations:
When selecting a tank size, it's important to account for headspace—the space above the liquid level in the fermenter. During fermentation, the yeast produces carbon dioxide, causing the wort to foam and rise. Adequate headspace prevents overflow and allows for proper fermentation without the risk of contamination. A good rule of thumb is to leave about 20-25% of the tank's capacity as headspace.
Scaling Up or Down:
Brewers who are scaling up from home brewing to commercial production must carefully consider how the increase in batch size will affect the fermentation process. Larger batches generate more heat during fermentation, requiring tanks with built-in temperature control systems. Similarly, those scaling down for pilot or experimental batches might choose smaller tanks that allow for greater flexibility and experimentation without the need for large quantities of raw materials.
What Are the Standard Sizes of Fermentation Tanks?
Fermentation tanks come in various standard sizes, catering to different scales of brewing. These sizes are typically measured in barrels (BBL) for commercial brewing or gallons for home brewing.
Home Brewing Tank Sizes:
- 1-Gallon to 3-Gallon Tanks: Suitable for very small or experimental batches.
- 5-Gallon to 10-Gallon Tanks: The most common sizes for home brewers, providing a balance between batch size and manageability.
- 15-Gallon to 20-Gallon Tanks: Used by more advanced home brewers who want to produce larger batches or split batches for different yeast strains or dry hopping experiments.
Commercial Brewing Tank Sizes:
- 3-BBL (93 Gallons): Ideal for small brewpubs or pilot batches in larger breweries.
- 7-BBL (217 Gallons): Common for microbreweries or small-scale production.
- 15-BBL (465 Gallons): Suitable for medium-sized breweries producing multiple batches per week.
- 30-BBL (930 Gallons): Used by larger breweries with a steady demand for their products.
- 60-BBL (1,860 Gallons) and Above: Reserved for large-scale breweries producing high volumes of beer.
Custom Sizes:
Some breweries opt for custom-sized tanks to meet specific production needs or to fit within unique brewery layouts. Custom tanks can be designed with specific features, such as dual-zone cooling or specialized ports for dry hopping, which might not be available in standard sizes.
How Does the Type of Beer Affect the Choice of Tank Size?
The style of beer being brewed can influence the choice of fermentation tank size. Different beer styles have varying fermentation requirements, which can impact the ideal tank size.
High-Gravity Beers:
Beers with a higher original gravity (OG), such as Imperial Stouts or Barleywines, require more space during fermentation due to the increased yeast activity and higher alcohol content. These beers may benefit from slightly larger tanks to accommodate the vigorous fermentation and the need for additional headspace.
Lagers vs. Ales:
Lagers typically require longer fermentation times at cooler temperatures, necessitating tanks that can maintain precise temperature control over extended periods. Because of this, lager breweries might prefer larger tanks that allow for longer storage times, reducing the need for frequent transfers between vessels. Ales, which ferment at warmer temperatures and usually have shorter fermentation times, may not require as large a tank, especially in smaller-scale operations.
Mixed Fermentation and Barrel-Aged Beers:
Brewers producing mixed fermentation or barrel-aged beers often use smaller tanks or barrels for these specialty products. The smaller size allows for greater control over the aging process and makes it easier to monitor the development of flavors over time. For these beers, tank size is often determined by the desired volume of the final product, taking into account the losses that occur during aging and conditioning.
What Are the Benefits and Drawbacks of Using Larger or Smaller Fermentation Tanks?
Choosing between larger and smaller fermentation tanks depends on various factors, including production goals, available space, and budget. Each option comes with its own set of advantages and disadvantages.
Benefits of Larger Tanks:
- Economies of Scale: Larger tanks allow for the production of more beer in a single batch, reducing labor and energy costs per unit of beer produced.
- Consistency: Producing larger batches can lead to more consistent results, as there is less variability between batches.
- Space Efficiency: In breweries with limited space, larger tanks can maximize production capacity without the need for additional vessels.
Drawbacks of Larger Tanks:
- Initial Cost: Larger tanks are more expensive to purchase and install, requiring a significant upfront investment.
- Maintenance: Larger tanks can be more challenging to clean and maintain, requiring specialized equipment or labor.
- Flexibility: Larger tanks may reduce the brewer's ability to experiment with different styles or small-batch releases, as each batch represents a significant volume of beer.
Benefits of Smaller Tanks:
- Flexibility: Smaller tanks allow for greater experimentation with different styles, yeast strains, and ingredients, making them ideal for pilot batches or limited releases.
- Lower Cost: Smaller tanks are less expensive to purchase and operate, making them more accessible for home brewers or small breweries.
- Ease of Use: Smaller tanks are easier to clean, move, and maintain, which can simplify the brewing process.
Drawbacks of Smaller Tanks:
- Limited Production: Smaller tanks produce less beer per batch, which can limit production capacity and increase per-unit costs.
- Inconsistency: With smaller batches, there is a greater potential for variability between batches, which can impact product consistency.
FAQs
- What is the recommended headspace for a fermentation tank?
- It is recommended to leave about 20-25% of the tank's capacity as headspace to accommodate the foam and carbon dioxide produced during fermentation.
- Can I use the same tank size for different types of beer?
- Yes, but it’s important to consider the specific fermentation requirements of each beer style, such as temperature control and fermentation time, which might influence the optimal tank size.
- How do I choose the right tank size for scaling up my production?
- When scaling up, consider factors such as your desired production volume, available space, budget, and the specific needs of the beers you plan to produce.
- Is it better to have multiple smaller tanks or a few larger tanks?
- This depends on your brewing goals. Multiple smaller tanks offer flexibility and the ability to experiment with different batches, while larger tanks provide economies of scale and consistency for high-volume production.