Prefab’s Second Life: Why Australia’s Backyard Boom Needs a Circular Makeover
- Written by Dave Warburton
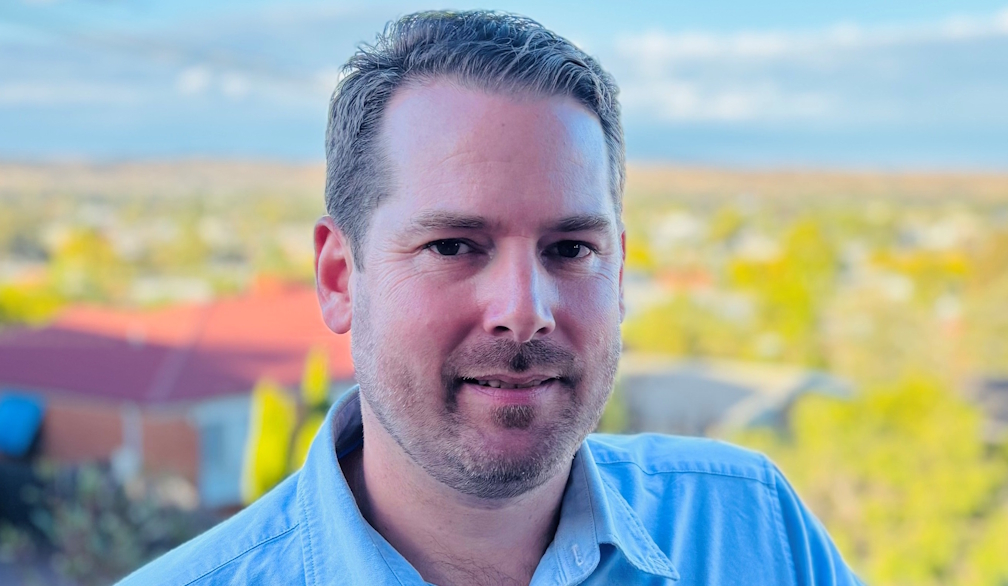
The humble granny flat is being reimagined not just as a fix for housing shortages, but as a cornerstone of circular, factory-built architecture. But are our systems ready to support it?
If the suburbs are Australia’s great frontier of affordable housing, then the backyard is its most underutilised asset. Granny flats—once a stopgap solution for ageing parents or adult children—are now front and centre in policy, finance, and design circles. What began as a convenience has evolved into a proposition for increasing urban density, supporting intergenerational living, and unlocking passive income in a sluggish economy. But there’s a quieter revolution happening alongside this popularity boom: the way these structures are being conceived, built and imagined for future use.
Granny flats, kit homes and other forms of small modular dwellings are no longer the domain of makeshift extensions or shipping-container chic. Instead, they are being refined in controlled environments, flat-packed with everything from plumbing to power points, and delivered to site in a matter of days. The ambition is clear—speed up approvals, reduce construction risk, and cut down cost—but there’s a bigger design opportunity lurking just beneath the surface: these homes could be built to come apart.
This is not the same as poor durability or temporary housing. What’s being proposed by some of the more forward-thinking architects and manufacturers is a modular ecosystem where components are designed to be removed, resold, and reused at the end of their initial life. Kitchens could become storage units. Roofing panels could be unbolted and remounted on the next build. Wall frames could be tracked through a digital passport that ensures safe recovery years down the line. This is design for disassembly (DfD)—an idea long explored in commercial and industrial buildings but only now creeping into the residential prefab conversation.
There’s good reason for the timing. As Australia prepares to roll out the 2025 update to the National Construction Code, with stronger emphasis on sustainability and lifecycle performance, a new framework for material reusability is forming. That means that the structural ingenuity of our future homes will no longer be judged solely by their insulation or orientation, but by what happens when they’re dismantled. In this context, a well-built granny flat is no longer just an add-on. It becomes a test lab for circular design at scale—smaller homes, shorter build times, and a clearer chain of custody for the resources embedded within them.
But turning theory into practice isn’t just a matter of swapping nails for bolts. Current systems—from planning overlays to financing structures—are not optimised for this kind of circularity. Many prefab and kit home providers still rely on glued assemblies, site-specific tweaks, and static materials that make reuse impractical. Lenders remain hesitant to underwrite relocatable structures unless tied to traditional land value. Councils may be relaxing rules on secondary dwellings, but few have considered what happens when those dwellings are moved, dismantled or repurposed elsewhere.
There’s also the issue of perception. Disassembly is often conflated with disposability, and small prefab homes can be misread as impermanent or unfit for mainstream housing markets. Yet some of the most resilient dwellings—particularly those designed to handle transport, wind load, and bushfire resistance—are those being produced off-site under rigorous quality controls. These homes aren’t fragile. They’re flexible. And that flexibility is what Australia needs most.
Housing supply is now a matter of urgency. Tens of thousands of families are locked out of homeownership. Vacancy rates remain at historic lows, especially in regional areas where land is abundant, but builders are stretched. Factory-built kit homes offer a partial reprieve. They don’t rely on stretched local trades. They can be assembled in days, not months. And with the right planning, they could be redeployed wherever demand spikes—reaching communities that would otherwise wait years for delivery of conventional stock.
It’s worth imagining how that ecosystem could work. A family in suburban Melbourne installs a certified, high-efficiency granny flat to support an elderly parent. Five years later, when that need changes, the structure is resold to a social housing provider who relocates it to a regional block outside Wodonga. Because the frame is modular, the transport is simple, and the materials carry verified product IDs, there's no guesswork. A reverse logistics pipeline already exists. The house gets a second life with minimal intervention. The original owner recoups a portion of their investment. The community gains a dwelling. No one sends timber to landfill. Everyone wins.
Of course, this level of coordination doesn’t happen overnight. It requires a shift in how we document, insure, and regulate housing stock. It will mean thinking about prefabrication not as a niche category, but as a central plank in Australia’s housing recovery. It will mean tracking materials with the same seriousness we track emissions. And it will mean broadening our definition of what a “home” is—less as a fixed address, and more as a mobile, modular asset that evolves with its occupants.
The technology is ready. Panelised walls with integrated conduits, bolt-on fixtures, cradle-to-cradle certified materials, and compact thermal bridges are all available and already in use in select pilot projects. Some manufacturers are even trialling buy-back schemes, where owners agree to return panels for reuse at a guaranteed rate—a kind of trade-in program for architecture. This is the kind of thinking that turns a simple granny flat into a building block for a larger, smarter system.
Whether the mainstream market will catch up in time is another question. But the next 12 months may prove pivotal. With finance unlocking, council overlays shifting, and demand for affordable options at an all-time high, the conditions are right for DfD modular homes to go from side-show to showcase. If the industry embraces this approach, we won’t just solve a housing shortage. We’ll start to build an architectural culture that is not only fast and efficient, but fundamentally regenerative.
And that’s the promise buried in today’s backyard builds. They’re not just structures for the here and now. They are blueprints for how we might live, design, and reuse in a future where nothing is ever truly thrown away.
http://www.ratechallenge.com.au/