Optimising Heavy Equipment Setup for Safety on Construction Sites
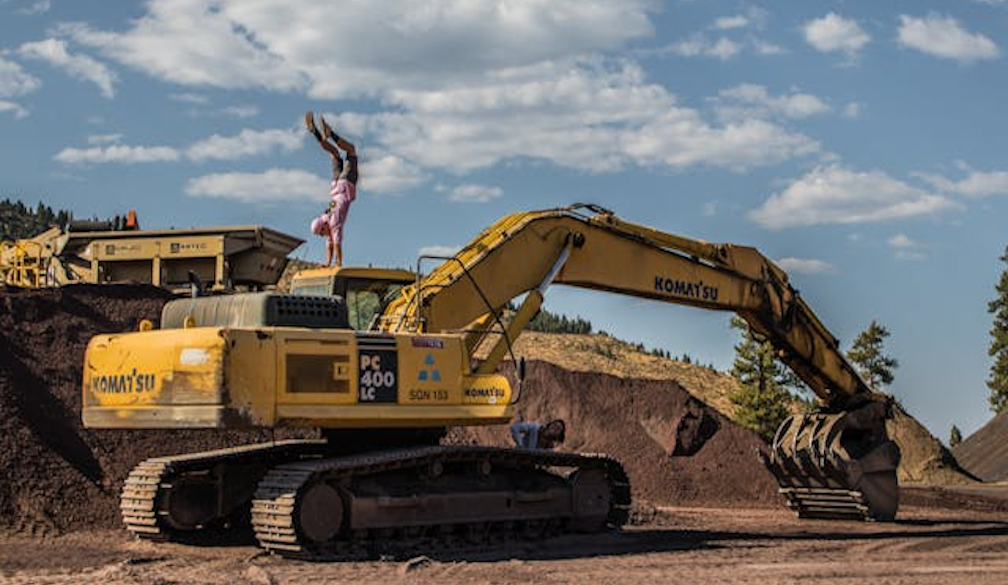
Safe heavy equipment operations are a crucial aspect of keeping a construction site incident-free. The way heavy machinery is set up directly impacts the safety of both the operator and nearby workers, and optimising this process can make all the difference. From choosing the proper location to employing effective training routines, there are several key practices that contribute to a safely organised workplace. Let's look into the key perspectives and importance of optimising heavy equipment setup to deliver maximal safety on construction sites. Read on.
Proper site inspection is the safety foundation
Before heavy equipment is brought on site, a careful inspection should be performed to identify potential hazards. Is the ground firm and level enough to support the machinery? Are there nearby slopes, drop-offs, or excavations that could undermine stability? Is there sufficient space for maneuvering without putting nearby workers or structures at risk? This initial evaluation sets the stage for everything that follows. Properly assessing soil conditions, slopes, and nearby obstructions helps avoid avoidable accidents stemming from equipment becoming unbalanced or tilting during operations.
Safe access
Safe entry and exit are frequently overlooked, yet they're a major contributor to injuries. Providing proper steps, grab handles, and non-slip surfaces helps reduce the likelihood of slips and falls while accessing heavy machinery. Furthermore, adding clear lighting or reflectors can aid visibility in low-light conditions, ensuring that both the operator and nearby workers can move safely. This may sound like a basic procedure, but it is surely one of the most crucial steps to perform when optimising heavy equipment for construction sites.
Implementing safe traffic control
Managing movement is key to reducing collision risk. Clearly marked pedestrian and vehicle routes enable heavy equipment to travel safely alongside workers and other vehicles. Cones, barriers, or fence lines can aid in guiding both the machinery and the people who work alongside it. Providing a well-planned flow for movement prevents confusion and minimises the chance of a collision. What is more, purchasing quality outrigger pads may aid in stabilising heavy equipment, especially when the ground is less than perfectly firm or level. These specialised supports help distribute the equipment’s weight more evenly, reducing pressure on weak soil and adding a crucial margin of safety for both the machinery and nearby workers.
Communication and training
Training is a powerful tool for reducing accidents. All heavy equipment operators should be trained not only in their own machinery’s controls but also in understanding signals, routines, and standard procedures. Furthermore, a clear communication plan, whether by radio, hand signals, or a designated spotter, helps team members avoid confusion and prevents catastrophic mistakes. Effective training also includes hazard recognition. An operator who is vigilant and able to identify potential problems before they become serious can make a huge contribution toward workplace safety.
Inspection and maintenance routines
One major cause of heavy equipment-related accidents is poor maintenance or a missed defect. Implementing a rigorous inspection routine, performed at the start of each day and after heavy use, helps identify problems before they manifest. Fluid levels, brakes, controls, and structural components should all be regularly examined, and repairs made promptly when issues arise. Proper maintenance guarantees the machinery performs safely and efficiently under pressure.
Implementation of collaborative safety culture
Creating a collaborative safety culture helps foster a workplace where everyone feels responsible for looking after each other’s well-being. Encourage team members to speak up when they see something that might pose a hazard, and make sure there’s a clear process for addressing those concerns. This collective vigilance helps identify potential problems long before they become accidents.
Strive for improvement
Continuous improvement is another key to optimising heavy equipment safety. After each incident or near miss, take the time to perform a brief root-cause analysis. This lets you learn from experience and implement new strategies to make future operations even safer. An adaptable, forward-thinking approach signals your team’s strong commitment to their own safety, which acts like a message that resonates across all phases of a project. When heavy equipment is set up and used with careful consideration, proper training, and ongoing vigilance, the result is a workplace where injuries are less likely, productivity increases, and team members feel valued and cared for.
Conclusion
Safe heavy equipment setup is not something that happens by accident; on the other hand, it’s the result of careful planning, vigilant routines, strong training, and a collective commitment to protecting everyone on the job site. When supervisors, operators, and workers collaborate toward the shared goal of a hazard-free workplace, the rewards are clear: reduced injuries, greater productivity, and a culture that values the well-being of all. Making safety a top priority from start to finish helps keep construction projects on track and sets a strong precedent for future operations.