Understanding Hard Chrome: What It Is, How It Works, and Why It Matters
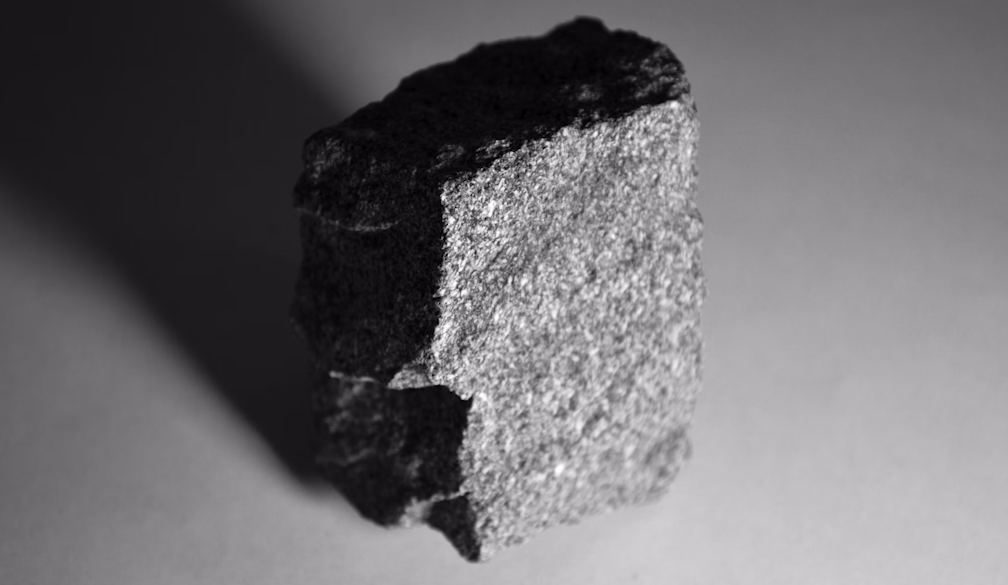
When it comes to industrial coatings, few materials offer the durability and performance of hard chrome. Known for its strength, wear resistance, and smooth finish, hard chrome plating is a go-to solution in industries where components must endure high friction, corrosion, or repeated mechanical stress. Whether you’re involved in manufacturing, automotive, aerospace, or heavy equipment, understanding how hard chrome works can help you make better decisions about protecting and enhancing metal surfaces.
What is Hard Chrome?
Hard chrome, also referred to as industrial chrome or engineered chrome, is a dense layer of chromium electroplated onto a metal substrate. Unlike decorative chrome—commonly seen on bathroom fittings or car parts—hard chrome is not used for aesthetic purposes. Instead, its primary role is to improve the functional performance of machine components.
The coating typically ranges in thickness from 20 to 500 microns, depending on the application. The deposition process involves immersing the part in a chromic acid solution and passing an electric current through it. The result is a hard, uniform layer of chromium that adheres strongly to the base metal.
Why Hard Chrome is Used
The biggest advantage of hard chrome lies in its wear and corrosion resistance. It significantly extends the service life of parts that would otherwise wear out quickly. Components like hydraulic cylinders, piston rods, rollers, shafts, and engine parts are often plated with hard chrome to withstand the stress of daily use.
Another key benefit is its low coefficient of friction. The surface becomes exceptionally smooth, reducing wear caused by contact with other materials. This also leads to lower operating temperatures and reduced energy loss due to friction—crucial for high-speed or high-pressure machinery.
Additionally, hard chrome can be used to repair worn or damaged components. Instead of replacing an expensive part, technicians can apply hard chrome to rebuild the surface and then machine it back to the required specifications. This not only saves money but also reduces downtime.
Applications Across Industries
The versatility of hard chrome makes it indispensable across various sectors. In the aerospace industry, it is used to coat landing gear and other structural components that face intense mechanical stress. The automotive sector relies on it for crankshafts, camshafts, and molds, where durability and dimensional precision are critical.
In the oil and gas industry, hard chrome is applied to drilling equipment and valves to resist corrosion in harsh environments. Manufacturing and printing industries use hard chrome on rollers and dies to maintain high performance over long production runs.
Food processing equipment and medical devices also benefit from hard chrome plating, thanks to its ease of cleaning and resistance to contaminants. However, in these sectors, coatings must comply with strict health and safety standards.
The Process of Applying Hard Chrome
Applying hard chrome is a detailed and precise operation. The surface to be coated must first be thoroughly cleaned to remove any contaminants. This can involve processes like degreasing, abrasive blasting, and chemical cleaning.
Once cleaned, the part is submerged in an electroplating bath containing a chromium solution. An electric current is then passed through the solution, causing chromium ions to bond with the metal surface. Controlling the voltage, temperature, and duration of the process ensures a uniform layer that meets exact specifications.
After plating, the component may require grinding or polishing to achieve the desired finish and dimensional accuracy. This step is crucial in high-tolerance applications where even slight deviations can affect performance.
Environmental and Health Considerations
While hard chrome offers numerous advantages, it's important to note that the process involves the use of hexavalent chromium—a known carcinogen. For this reason, the industry is heavily regulated, and facilities must follow strict environmental and safety protocols to minimize exposure risks.
New technologies and alternative coatings are being explored, but hard chrome remains widely used due to its unmatched properties. Many modern facilities have adopted advanced air filtration and waste management systems to continue using hard chrome responsibly and sustainably.
Maintenance and Longevity
One of the reasons industries continue to rely on hard chrome is its long-lasting performance. With proper maintenance, hard chrome coatings can extend the lifespan of machinery by several years. Periodic inspections can help identify early signs of wear or damage, allowing for timely re-plating or polishing to restore optimal function.
The coating’s resistance to corrosion also means that components are less likely to degrade over time, especially in environments with moisture, chemicals, or temperature fluctuations. This makes hard chrome a cost-effective investment in the long run.
Final Thoughts
Despite growing interest in alternative surface treatments, hard chrome continues to set the standard for wear resistance, surface hardness, and corrosion protection in demanding industrial settings. Its ability to restore, protect, and extend the life of critical components keeps it at the forefront of engineering solutions.
Whether you're looking to maintain high-value equipment or improve the performance of moving parts, understanding the role and capabilities of hard chrome can help you make smarter, more cost-effective decisions. As technology and environmental standards evolve, the future of hard chrome will likely focus on making the process safer and more efficient—without sacrificing the performance it’s known for.