Install Heating Ducts in Your Own Place to Stay Warm and Cozy
- Written by NewsServices.com
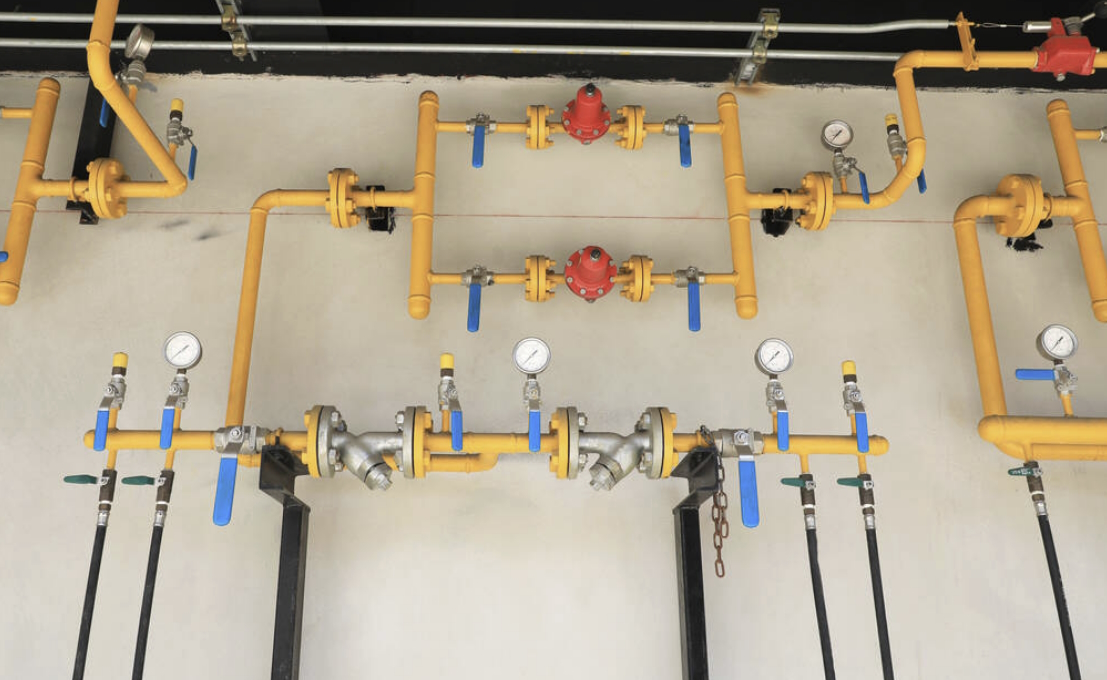
Gather the necessary materials and tools for installation
If you are about to begin an installation project, it is essential to have the right materials and tools on hand before starting. Having the proper supplies can help ensure that your project goes smoothly and that you have a successful outcome. Here are some tips for gathering the necessary materials and tools for installation.
The first step is to create a list of all of the items needed for your installation project, including any accessories or hardware that may be required. Make sure to include items such as screws, nails, brackets, hinges, pipes, fittings, and other pieces of hardware required for assembling or attaching components. Also, include any specialized tools needed in order to complete your tasks such as an electric drill or saws.
Once you’ve created a comprehensive list of items necessary for completing your job it’s time to gather them together in one place. This will make assembling components much easier since you won't need to search around or go back and forth between different stores looking for different parts or pieces. Depending on what type of material is being used in your project it may be best to purchase everything from one source so that all parts match up perfectly with each other without having inconsistencies from different manufacturers or suppliers. Ducted heating installation Melbourne is your one-stop solution to keep your home or office warm and comfortable during the colder months.
Prepare the space for installation, including measuring and cutting any holes needed in walls or floor.
Preparing a space for installation is an important step in any remodeling project, as it ensures that you end up with a perfectly finished product. While the exact requirements of your project will vary depending on what you’re installing, there are some important steps that should be taken to help ensure success.
When preparing the space for installation, it is essential to accurately measure and cut any necessary holes in the walls or floor. This will ensure that the item fits perfectly without having to make any adjustments after installation or risk damaging other surfaces. If possible, use a jigsaw or drill to cut your holes so they have smooth edges and fit snugly around your item. If you are unable to do this yourself, then hiring a professional can help save time and ensure accuracy when setting up your project area.
Once all of the necessary cuts have been made, it’s time to start assembling whatever needs assembly before beginning installation. Read through all directions carefully and make sure all pieces are present before beginning assembly as this can save time when it comes time for actual installation later on. Once everything has been assembled correctly move on to securing any items into place using screws or anchors if necessary so that they stay securely in place once installed properly into their designated position within the wall.
Determine a plan for routing the ducts from the furnace to each room.
Routing ducts from a furnace to each room in a home can be an intimidating task for homeowners who are unfamiliar with HVAC systems. But with a plan and the right tools, this job can be completed quickly and efficiently. Here is how to determine and execute an effective plan for routing the ducts from the furnace to each room.
Step One: Map Out Your Home
The first step in creating your routing plan is mapping out your home. A good place to start is by drawing out the floor plan of your home on paper or using an online tool like RoomSketcher. Include all of the rooms that need heating as well as any obstacles such as walls, stairs, closets, etc. This will help you visualize how best to route your ducts throughout the house so that each room gets adequate heat distribution.
Step Two: Select Duct Material
Once you have mapped out your home and determined where you will need ducts running through, it’s time to select which type of material you want for your ductwork system. There are several options available ranging from metal flexible tubing to rigid PVC piping - depending on what type of installation you have in mind for your particular space requirements and budget constraints.
Install the main supply trunk from the furnace to each room.
Installing the main supply trunk from the furnace to each room is an important part of setting up a heating system. This process, while not overly complicated, requires some knowledge and skill in order to be done correctly. In this article, we will discuss the basics of how to install the main supply trunk from your furnace to each room in your home.
The first step is to determine where your furnace is located and identify where you would like each room’s primary air ducting outlets will be located in relation to it. Once you have determined these locations, you can then begin measuring and cutting the necessary pieces of ductwork for installation (if needed). It’s important that all pieces are cut precisely so that they fit together properly when installed.
Once all of your pieces are cut and ready for installation, you can now move on to actually installing them onto your furnace unit. Start by attaching one end of the main supply trunk directly onto the output port on top of your furnace unit and secure it with screws or bolts as needed. Make sure that this connection is tight enough so no air leaks occur when running or turning on/off your heating system later on down the road.
Connect branch lines to supply each individual register in each room.
When it comes to boosting efficiency in the workplace, one of the most important elements is having a well-organized and efficient network of branch lines that supply each individual register in each room. This type of setup ensures that the product can be quickly accessed and handled with minimal disruption or delay. It also reduces the amount of time needed for staff to move around between registers, allowing them to focus on customer service and other tasks.
A properly designed branch line network should contain multiple lines that lead from a main source such as a storage area or distribution center straight into each individual register. This allows employees to have easy access to whatever items they need without having to search through several areas for them. Depending on the size and complexity of the business, there may need to be multiple branches leading out from a single source in order to ensure adequate coverage throughout all areas of operation. In addition, it’s important that these lines are clearly marked so staff can easily identify which branch leads were without any confusion.
Having well-connected branch lines can also help save money by eliminating unnecessary movement between registers when products are needed urgently or when higher volumes are expected during certain times such as peak sales hours.
Secure all ducts with support clamps, as needed.
When it comes to keeping your home safe and efficient, securing all ducts is an essential part of the process. Ducts play a vital role in distributing air throughout a home, and if they are not properly secured, air can leak out of the system and cause energy efficiency to suffer. Fortunately, support clamps are an easy way to ensure that your ducts remain secure.
The first step in using support clamps is identifying where they should be placed. Look for any loose or sagging sections of ductwork which could benefit from additional stability. Once you’ve located these areas, you’ll need to measure the size of each section so that you can choose the appropriate clamp size for each application. It is important to use clamps that fit snugly around the entire circumference of the ductwork so that there isn’t any excess space between them and the metal surface; this will provide a more secure seal which helps prevent air leakage from occurring.
Once you have chosen the correct clamp sizes for each section, it’s time to install them onto your system. Start by positioning yourself so that you have access to both sides of the joint where two pieces of ductwork come together.
Seal any seams with mastic or foil tape.
When it comes to making sure your home is sealed and properly insulated, one of the most important steps you can take is to seal any seams with mastic or foil tape. These two products offer superior insulation by creating an airtight barrier around the area. The benefits of sealing seams with mastic and/or foil tape are numerous, from energy savings to increased comfort levels in your home.
Mastic is a type of liquid adhesive that dries into a hard, waterproof sealant when applied to a surface. It can be used on all types of materials including wood, metal, plastic, and concrete. Mastic seals against air infiltration, which can dramatically reduce the amount of energy lost through drafts in your home. It also provides superior soundproofing capabilities since it blocks out outside noise more effectively than other adhesives or tapes.
Foil tape is a specialized type of adhesive designed specifically for sealing seams where insulation may be present or needed in order to prevent condensation buildup within walls or other areas where moisture could become trapped behind drywall or other materials used in construction projects. Foil tapes are designed with strong adhesion properties and reflective surfaces that create an effective barrier against heat transfer as well as block out outside noise more effectively than standard duct tape products.
Test the operation of the system and adjust as necessary.
Testing and adjusting the operation of a system is an important part of ensuring that it functions properly. Whether it's a computer system, a mechanical device, or any other type of system, testing its operation and making adjustments as necessary are essential steps in keeping it running optimally.
When testing the operation of a system, the first step is to identify what needs to be tested. For example, if you are testing the performance of a computer system, you would need to measure the speed at which it processes data and how quickly its output can be displayed on the screen. Once you've identified what needs to be tested, you can then begin running tests on different parts of the system in order to determine how they are performing compared to their expected results.
Once testing has been completed, adjustments may need to be made in order for the system's performance to meet its desired goals. This could include anything from changing settings on software or hardware components to replacing certain components altogether if they are found to be faulty or outdated. In addition, some systems may require regular maintenance such as cleaning or lubrication in order for them to continue functioning correctly over time.