How a concrete alternative can cut emissions, resource use and waste
- Written by Aliakbar Gholampour, Senior Lecturer in Civil and Structural Engineering, Flinders University
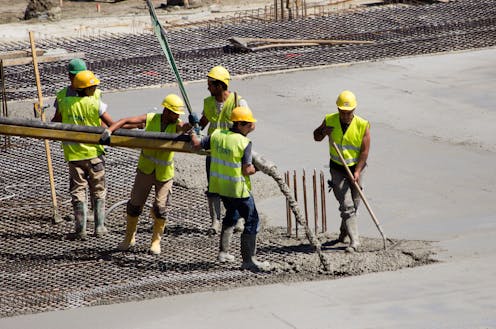
Building materials and construction generate about 20%[1] of global greenhouse gas emissions[2]. Much of these emissions are due to the environmentally unfriendly process of producing ordinary Portland cement[3], which is widely used in construction materials such as concrete and mortar.
Portland cement production generates about 2.6 billion tonnes of carbon dioxide (CO₂) a year – more than 7%[4] of annual global emissions. Cement emissions have doubled in the past 20 years[5]. And over the next 40 years, construction is expected to double the building floor area[6] worldwide.
Read more: Buildings produce 25% of Australia's emissions. What will it take to make them 'green' – and who'll pay?[7]
Every tonne of cement produced also uses about 1.6 tonnes of raw materials[8], including fuels and other resources. Concrete production also uses large amounts of aggregate such as sand and gravel. This requires energy-intensive quarrying operations that deplete non-renewable natural resources[9] – the world is running out of building sand[10].
The problems of emissions and resource depletion mean suitable substitutes for Portland cement and natural aggregate are required. Our research[11] shows it is possible to develop more sustainable construction materials, reinforced using natural fibres. Industrial byproducts and waste materials can be used to replace cement binder and aggregate, reducing emissions, resource depletion and waste.
Read more: Green cement a step closer to being a game-changer for construction emissions[12]
Recycling cuts waste
Recycling waste materials in construction can help reduce the environmental impacts of concrete and mortar production and the disposal of waste materials in landfills.
These materials include industrial byproducts (fly ash and blast furnace slag), waste glass and lead slag. Fly ash comes from coal-fired power stations. Blast furnace slag is a byproduct of iron and steel production.
A new type of eco-friendly material, geopolymer[13], has received significant attention as a replacement for conventional concrete. A geopolymer is a hard and durable human-made substance. Geopolymer production produces up to 90% less CO₂ emissions[14] than conventional concrete.
The properties of waste glass and lead slag make them suitable for use in making geopolymer.
Read more: Australia needs construction waste recycling plants — but locals first need to be won over[15]
Natural fibre reinforcement is sustainable
Steel or other synthetic fibres have been widely used as reinforcement material to improve the mechanical properties of geopolymer. However, steel fibres are expensive and corrode in harsh environments.
The synthetic alternative, mineral fibres, such as polyvinyl alcohol and polypropylene, are produced using antioxidants and amines. This process makes these fibres a non-eco-friendly material.
Natural fibres obtained from plants are a viable alternative to non-renewable, corrosive and expensive synthetic fibres. Natural fibres are renewable, eco-friendly, non-corrosive, cheap and abundant. These properties make natural fibres a sustainable material.
What did the study find?
Any substitutes for the concrete and mortar used today should at least match their engineering properties, such as strength and durability. Our study[16] evaluated the production and performance of geopolymers made with waste glass and lead slag instead of natural sand. We used a combination of fly ash and granulated blast furnace slag as binders instead of Portland cement.
These geopolymers were reinforced with different types of natural fibres such as coir[17], ramie[18], sisal[19], hemp[20], jute[21] and bamboo[22] fibres.
Our experimental results showed geopolymers containing waste glass sand have higher strength and absorb less water than those containing lead slag and natural sand. Water absorption reduces the durability of concrete.
Geopolymers prepared with lead slag show a lower drying shrinkage than geopolymers made with waste glass sand and lead slag. Drying shrinkage also reduces durability, as it leads to cracks in the concrete before it bears any kind of load.
We found that geopolymers with 1% ramie, hemp and bamboo fibre have greater compressive and tensile strengths than unreinforced geopolymers. This means the reinforced geopolymer resists breaking when squeezed (under compression loading) and when pulled apart (under tension loading). The higher strength of natural fibre-reinforced mixes is because of the bridging effect of the fibres inside the geopolymer.
Our study also shows that ramie, hemp and bamboo fibre-reinforced geopolymers shrink less than unreinforced geopolymers.
Read more: Greening the concrete jungle: how to make environmentally friendly cement[23]
What next?
The next steps in this research would include study of:
Read more: Future cities could be 3D printed – using concrete made with recycled glass[24]
Developing sustainable concrete will provide us with a next-generation construction material that greatly improves the sector’s resource efficiency while reducing its emissions and other environmental impacts.
References
- ^ about 20% (architecture2030.org)
- ^ global greenhouse gas emissions (www.ipcc.ch)
- ^ Portland cement (www.britannica.com)
- ^ more than 7% (phys.org)
- ^ doubled in the past 20 years (phys.org)
- ^ double the building floor area (www.worldgbc.org)
- ^ Buildings produce 25% of Australia's emissions. What will it take to make them 'green' – and who'll pay? (theconversation.com)
- ^ 1.6 tonnes of raw materials (www.buildinggreen.com)
- ^ deplete non-renewable natural resources (www.conserve-energy-future.com)
- ^ running out of building sand (www.bbc.com)
- ^ Our research (www.sciencedirect.com)
- ^ Green cement a step closer to being a game-changer for construction emissions (theconversation.com)
- ^ geopolymer (www.geopolymer.org)
- ^ 90% less CO₂ emissions (www.geopolymertech.com)
- ^ Australia needs construction waste recycling plants — but locals first need to be won over (theconversation.com)
- ^ Our study (www.sciencedirect.com)
- ^ coir (ecoworldonline.com)
- ^ ramie (ecoworldonline.com)
- ^ sisal (edition.cnn.com)
- ^ hemp (cfda.com)
- ^ jute (www.recycledmats.com.au)
- ^ bamboo (ecoworldonline.com)
- ^ Greening the concrete jungle: how to make environmentally friendly cement (theconversation.com)
- ^ Future cities could be 3D printed – using concrete made with recycled glass (theconversation.com)