Shuttered car factories in Australia could be repurposed to make houses faster and cheaper
- Written by Ehsan Noroozinejad, Senior Researcher, Urban Transformations Research Centre, Western Sydney University
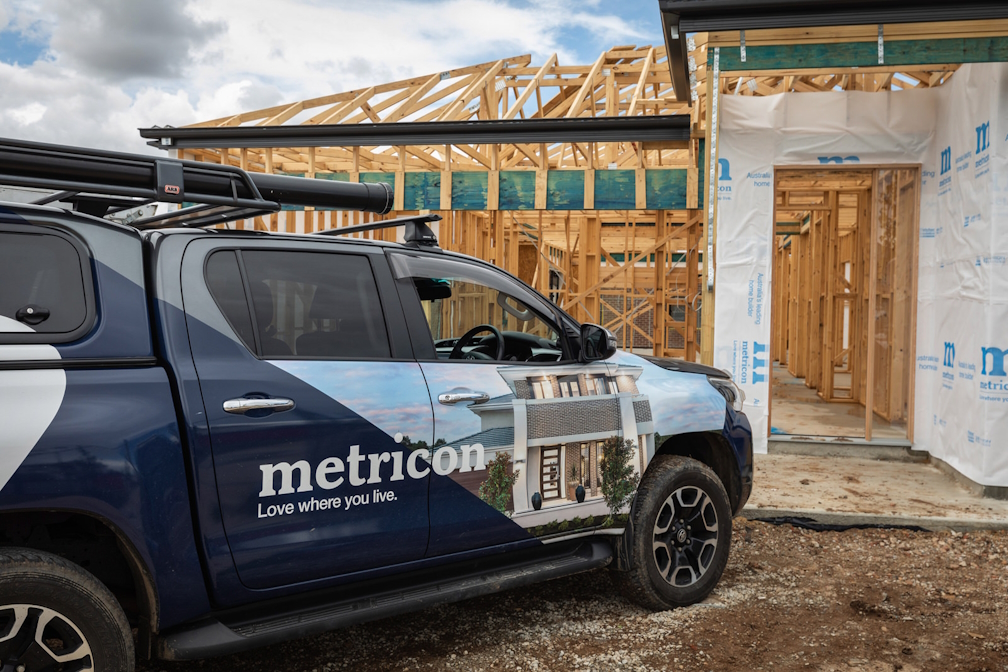
Australia is in the grip of a severe housing shortage[1]. Many people are finding it extremely difficult to find a place to live in the face of rising rents and property price surges. Homelessness is rising sharply. Tent cities are becoming more common.
The federal government has pledged to encourage the building of about 1.2 million new dwellings over the five years[2] from mid-2024. The problem is, conventional building techniques are unlikely to be able to respond to the scale of demand quickly. Conventional building is expensive and slow. Faster, cheaper construction methods are needed[3].
There might be a way to accelerate the build. In recent years, car manufacturers Ford, General Motors and Toyota have shuttered[4] their Australian factories, due to intense global competition[5].
Before these factories fell silent, they were home to trained workers, advanced machinery and efficient production systems. In Australia, companies such as Hickory Group are working[6] to turn car factories into house factories. In Japan, Toyota has been making[7] modular housing for decades, by adapting car production line techniques.
Scaling this approach up in Australia could simultaneously address industrial decline and housing demand.
Can mothballed car factories really make houses?
After years of decline, Australia’s car manufacturing industry came to an end[9] in 2017, when Toyota and General Motors’ factories stopped mass production. Ford’s local factories closed a year earlier. It was the end of 70 years of mass production, though companies such as Premcar are still making[10] local versions of overseas cars.
Thousands of factory workers lost their jobs. But the effect rippled outward, as about 40,000 workers in the supply chain lost their jobs[11].
These automobile factories left behind more than just empty structures[12].
Most of them have not been demolished. Some still have advanced manufacturing lines. Their former workers with automation and precise engineering training might be working in different fields, such as caravan manufacturing.
Building a house in a factory has similarities to car manufacturing. Both use modular production, in which individual parts are manufactured and then assembled into a final product.
That’s not to say this would be easy – there would be regulatory hurdles to overcome and the factories would need an overhaul.
One tough part is figuring out how to use modern car-building tools (such as robotics) to make components of houses. While building cars and houses share some ideas, they’re not the same.
Bringing these factories back into production would boost[13] the economies of states such as Victoria.
States such as South Australia have already started down this path, turning Mitsubishi’s defunct Tonsley Park factory into an innovation precinct hosting modular construction companies such as Fusco Constructions[14], which will begin operations next year.
Meanwhile, much work has been done[15] in Australia and overseas to find ways to mass-produce housing using factories.
Imagine thousands of individual car parts were delivered to your front yard, where workers painstakingly put the car together. This seems crazy. But it’s essentially what we do with houses, especially freestanding ones. Advocates for modern methods of construction have pointed out[16] the inefficiencies of transporting building materials to a site and assembling them there.
Some large-scale builders are already working to automate[17] more of the home-building process. Besides making houses more cheaply, the benefits include centralising production around a factory, protection from weather delays, and the ability to use industrial robots.
Car assembly lines guarantee each component is manufactured to exacting specifications. Automobile manufacturing has been transformed by new technologies, including digital twin simulations, robotics and 3D printing. But the building industry has been slower to take these up. If we can bring these technologies to bear[18] on how we make homes, we can accelerate construction, reduce errors and cut prices.
In fact, we are seeing some car manufacturers moving into home building. Mercedes-Benz, Bugatti, Bentley, Aston Martin and Porsche are all putting their names[19] on high-end homes in some way, while Honda has explored[20] manufacturing smart, low-energy homes.
Change is coming – but slowly
Advanced building techniques are not new to Australia. Prefab buildings[22] are already being built on factory lines by companies such as Fleetwood, ATCO Structures and Logistics and Modscape.
Here, building components are produced in a controlled factory setting before being delivered to the construction site for prompt assembly. Dozens of companies are working[23] in this space. To date, however, most of these buildings will be used as schools, police stations or temporary housing for mining workers.
Last year, the federal government set up a A$900 million fund[24] as an incentive for state and territory governments to accelerate building approvals and take up prefab techniques. To date, the sector is struggling to scale up[25] due to a lack of infrastructure and too few manufacturers.
Other countries are further along the path. In Sweden, up to 84% of detached homes are made with prefabricated components[26], compared with about 15% in Japan and 5% in the United States, United Kingdom and Australia.
One option is to adopt yet more advanced techniques, such as lean manufacturing[27] and automated assembly. Both of these are well established in car-making, and could be used to increase the speed and accuracy of prefab home construction.
What would it take to make this happen?
Australia’s housing crisis has been years in the making. To solve it, we may need bold solutions.
Converting old car factories into affordable home factories could help accelerate our response to the challenge – and reinvigorate industrial precincts.
It would take work and funding to make this happen. But there are commonalities. Making prefab homes depends on precise, modular production methods that work best when automated. Transitions like these can happen.
References
- ^ severe housing shortage (stories.uq.edu.au)
- ^ five years (treasury.gov.au)
- ^ are needed (thepolicymaker.jmi.org.au)
- ^ have shuttered (www.pc.gov.au)
- ^ intense global competition (theconversation.com)
- ^ are working (www.hickory.com.au)
- ^ been making (www.construction-physics.com)
- ^ Kelly Barnes/AAP (photos.aap.com.au)
- ^ came to an end (www.tandfonline.com)
- ^ still making (premcar.au)
- ^ lost their jobs (www.pc.gov.au)
- ^ empty structures (www.abc.net.au)
- ^ would boost (australiainstitute.org.au)
- ^ Fusco Constructions (tonsley.com.au)
- ^ has been done (theconversation.com)
- ^ pointed out (www.autodesk.com)
- ^ working to automate (www.afr.com)
- ^ to bear (issuu.com)
- ^ putting their names (www.forbes.com)
- ^ has explored (smarthome.honda.com)
- ^ Queensland Government/AAP (photos.aap.com.au)
- ^ Prefab buildings (theconversation.com)
- ^ are working (www.prefabaus.org.au)
- ^ A$900 million fund (www.abc.net.au)
- ^ struggling to scale up (www.abc.net.au)
- ^ prefabricated components (architizer.com)
- ^ lean manufacturing (www.build-review.com)